The second iconic work spot of the summer was 2-weeks of mast building at Shaw & Tenney. Shaw and Tenney has been in business since 1858 making gorgeous paddles and oars as well as masts, boat hooks, etc for boats. Sometimes they get interesting orders like for this project building four 8" diameter laminated, Douglas Fir masts for a high-end playground in NYC. They asked me to come up and help them take on this project and I was happy to do it.
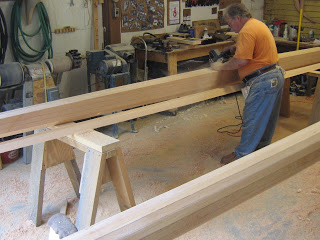
The masts were all cut, rounded, and sanded by hand. They weight a few hundred pounds in the rough and were a challenge to put through the planer. Their dimensions had to be very accurate. Like any mast, once the piece is 4-sided and tapered, we can start 8-siding as we are doing above with a small skilsaw. After 8-siding this way, the mast was brought to 128-siding with nothing but patience and my favorite power planer. After two days plus of the power planer, when I that machine down for good, I can recall my hand vibrating for several hours.
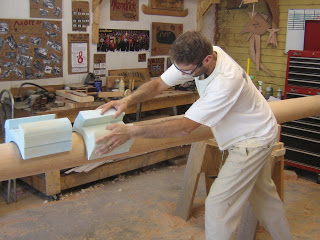
The final rounding was done with custom shaped foam blocks, a trick from boat school that I use on a lot of projects. This was followed by finish sanding with the Festool. The result was some very nice masts! It was a wonderful place to work and watch the masters do their trade. One of the guys has been making oars and paddles for 25 years. To watch him work was quite impressive. I look forward to doing more business with S & T. Recently, they chose Clint Chase Boatbuilder as their official builder of their beautiful Whitehall.
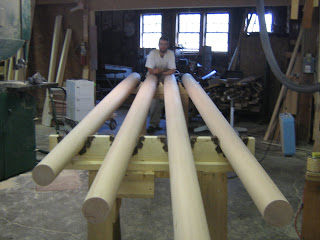
After this project it was back to Portland for an overnight to see the family and pack for the next iconic week: Wooden Boat in Brooklin, Maine. I was to make my teaching debut at the Wooden Boat School.
The masts were all cut, rounded, and sanded by hand. They weight a few hundred pounds in the rough and were a challenge to put through the planer. Their dimensions had to be very accurate. Like any mast, once the piece is 4-sided and tapered, we can start 8-siding as we are doing above with a small skilsaw. After 8-siding this way, the mast was brought to 128-siding with nothing but patience and my favorite power planer. After two days plus of the power planer, when I that machine down for good, I can recall my hand vibrating for several hours.
The final rounding was done with custom shaped foam blocks, a trick from boat school that I use on a lot of projects. This was followed by finish sanding with the Festool. The result was some very nice masts! It was a wonderful place to work and watch the masters do their trade. One of the guys has been making oars and paddles for 25 years. To watch him work was quite impressive. I look forward to doing more business with S & T. Recently, they chose Clint Chase Boatbuilder as their official builder of their beautiful Whitehall.
After this project it was back to Portland for an overnight to see the family and pack for the next iconic week: Wooden Boat in Brooklin, Maine. I was to make my teaching debut at the Wooden Boat School.